Brass, a widely used metal alloy composed of copper and zinc, finds applications in various industries. Understanding its magnetic properties, including paramagnetic metals, ferromagnetic metals, and electron spin, is crucial due to the practical implications it holds. The intriguing relationship between brass and magnetism, magnetic attraction, paramagnetic metals, permanent magnetic has piqued the interest of many. Despite being primarily non-magnetic as a type of metal, brass can exhibit some magnetic properties when in the presence of other magnetic materials such as nickel or iron. This characteristic makes stainless steels valuable for specific applications like door holders or pieces requiring both strength and corrosion resistance.
The historical context of metals and their magnetic properties, electrons, dates back centuries, with ongoing developments shedding light on new discoveries about these materials’ behavior under different conditions.
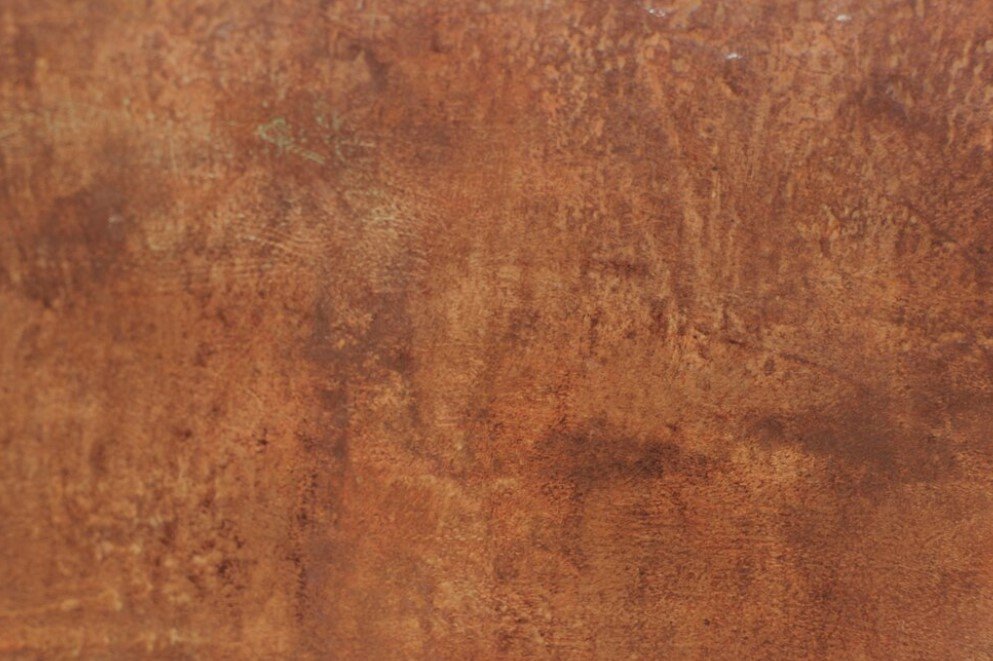
Understanding the Composition of Brass
Copper and Zinc
Brass, a popular metal alloy, is primarily composed of copper and zinc. The varying proportions of these two metals result in different types of brass alloys. Some brasses have higher copper content, while others contain more zinc.
The composition of metals directly influences the physical properties of the alloy, including its magnetic behavior. high-copper brass metal is not magnetic due to the non-magnetic nature of copper. On the other hand, some brass alloys with a higher proportion of zinc can exhibit weak magnetic properties.
Impurities’ Influence
Impurities present in brass alloys, metal, bronze, can also significantly impact their magnetic properties. Small amounts of iron impurities can make certain brass compositions slightly magnetic.
These impurities act as “contaminants” within the metal alloy structure, affecting its overall magnetism. Even though pure brass itself isn’t inherently magnetic due to its copper content, impure variations may display minimal attraction to magnets due to these added elements.
The Fundamentals of Magnetism
What is Magnetism?
Magnetism is the force exerted by magnets, attracting or repelling materials. It’s like a magical invisible force that pulls some things together and pushes others apart. /// This phenomenon occurs due to the movement of electric charges, creating magnetic fields around them.
When you think about magnetism, picture tiny particles inside an object all lined up in the same direction. These aligned particles create a magnetic field around the object, making it act like a magnet itself.
The Role of Magnetism in Brass
Now, let’s circle back to our main question: “Is brass a magnetic material?” Well,We encounter an interesting twist. Although brass, which is primarily made up of copper and zinc, isn’t inherently magnetic because neither copper nor zinc are magnetic elements; however…
…there’s always a ‘but.’ If you take this non-magnetic brass and place it near a strong magnet, something intriguing happens. Even though brass doesn’t get attracted to magnets under normal circumstances, if you bring it close to a strong enough one—like those made from neodymium—brass will interact with the magnetic field.
This interaction isn’t because brass becomes magnetic but rather due to what we call “electrical conductivity.” When exposed to powerful magnets or moving through their fields (as can happen during recycling processes), electric currents known as eddy currents are induced within non-magnetic materials such as brass.
These eddy currents then produce their own opposing magnetic fields which cause slight interactions between the material and the original strong magnet. So while pure brass isn’t considered a permanent magnet, its electrical properties allow for these fascinating albeit temporary interactions with strong magnets.
Distinguishing Magnetic and Non-Magnetic Materials
Understanding Magnetism
Magnetic materials are substances that can be magnetized, exhibiting magnetic properties. When exposed to a magnetic field, these materials become magnetized themselves. On the other hand, non-magnetic materials do not retain any magnetization once removed from a magnetic field.
Magnetism is an essential property of certain elements and alloys like iron, nickel, and cobalt./// These elements possess ferromagnetic properties, meaning they can be permanently magnetized. Identifying whether a material is magnetic or non-magnetic is crucial for various applications in everyday life.
Understanding how different types of materials respond to magnets helps in creating devices such as door stops and other products that rely on their magnetic nature.
Applications of Magnetic Materials
In the realm of technology, numerous devices utilize the principles of magnetism and magnetic field. From refrigerator magnets to complex computer hard drives, magnetic metals play a vital role in modern electronic gadgets.
For instance:
Hard disk drives use ferromagnetic materials to store data through changes in their magnetic orientation.
Electric motors function by interacting with permanent magnets made from specific ferromagnetic alloys.
Furthermore, distinguishing between magnetic and non-magnetic materials ensures safety in various scenarios. For example:
In construction projects where heavy machinery relies on powerful electromagnets for lifting operations.
In medical settings where MRI machines employ strong magnetic fields for diagnostic imaging purposes.
How Alloying Affects Magnetic Properties
Impact of Alloying
Alloying plays a crucial role in determining whether brass is a magnetic material. By adding specific elements to brass, its magnetic behavior can be influenced. For example, the addition of iron to brass can make it more susceptible to magnetization. On the other hand, when aluminum or manganese is added to brass, it becomes less magnetic.
The presence of these alloying elements alters the arrangement and movement of atoms within the brass structure, affecting its response to magnetic fields. This means that even though brass is primarily composed of copper and zinc, the introduction of other elements during alloying can significantly impact its magnetic properties.
Adding iron to brass creates an alloy known as “ferrous brass,” which exhibits stronger magnetic characteristics compared to standard brass due to the ferromagnetic nature of iron. Conversely, incorporating non-magnetic elements like aluminum or manganese into brass reduces its overall magnetism.
Process Significance
The process of alloying holds substantial significance in understanding why brass may exhibit varying degrees of magnetism. When different metals and neo magnets are combined through alloying techniques such as melting and mixing at specific temperatures, their individual properties interact and influence each other’s behavior.
For instance, when iron is introduced during the alloying process for making ferrous brass, it becomes an integral part of the resulting material’s composition. This integration directly impacts how susceptible the final product will be to magnetic forces.
Similarly, by carefully controlling and manipulating various parameters during alloy production—such as temperature settings and metal ratios—the desired level of magnetism in brass alloys can be achieved based on specific application requirements.
Common Uses of Brass in Industry
Non-Magnetic Properties
Brass, a metal alloy composed of copper and zinc, is widely used across various industries due to its non-magnetic properties. Unlike materials like iron or steel, brass does not exhibit any significant magnetic attraction. This makes it highly suitable for applications where magnetism can interfere with the functionality of the components or products.
Brass’s non-magnetic nature makes it an ideal choice for manufacturing electrical components and equipment. For instance, in electrical connectors and terminals, the absence of magnetic properties prevents interference with the flow of electric current. In environments where magnetic fields need to be controlled or minimized – such as in sensitive electronic devices – brass serves as an essential material due to its non-magnetic characteristics.
In plumbing systems, brass fittings are preferred over ferromagnetic materials because they do not interfere with the operation of tools and equipment that rely on magnetism for detection or alignment. The non-magnetic nature also ensures that these fittings do not disrupt compass readings when installed near navigation instruments on marine vessels.
Diverse Industrial Applications
The applications of brass extend beyond its non-magnetic properties; this versatile alloy finds widespread use across diverse industrial sectors. In addition to plumbing and electrical applications, brass is commonly employed in manufacturing decorative items such as jewelry, ornaments, and architectural hardware.
Furthermore, due to its excellent malleability and resistance to corrosion from moisture exposure (such as seawater), brass is extensively utilized in marine engineering for producing valves, pumps, propellers shafts among others.
Musical instruments also heavily feature brass components owing to their unique acoustic properties alongside resistance against corrosion from prolonged contact with breath moisture during playing.
Brass’s non-magnetism allows it to be used effectively alongside magnet-sensitive technologies.
Its uses span from practical applications like plumbing fittings to more aesthetic purposes like ornamental decorations.
The versatility stems from both its physical attributes (like malleability) and chemical ones (resistance against corrosion).
Testing Brass for Magnetic Properties
Methods of Testing
There are various methods available. One common method involves using a magnet to determine if the brass is magnetic. If the brass is attracted to the magnet, it indicates that it contains some level of ferromagnetic materials.
Another method includes utilizing specialized equipment such as a gauss meter or a fluxmeter. These tools can provide more precise measurements of magnetic pull strength and help in determining the exact magnetic properties of the brass.
These testing methods are crucial in ensuring that the brass meets specific requirements for its intended application. For instance, in industries where non-magnetic properties are essential, accurate testing helps in identifying suitable brass materials that won’t interfere with sensitive equipment or electronic devices.
Importance of Accurate Testing
Accurate testing procedures play a crucial role in determining the suitability of brass for different purposes. For example, in electrical applications where non-magnetic characteristics are vital, rigorous testing ensures that only non-magnetic or weakly magnetic brass alloys are used to prevent interference with electrical currents and fields.
Moreover, accurate testing also guarantees compliance with industry standards and regulations. By verifying the magnetic pull strength and other magnetic properties through reliable testing methods, manufacturers can ensure that their products meet quality control standards and perform optimally within their intended environments.
Alternatives to Brass for Magnetic Applications
Stronger Alloys
Some alloys, unlike brass, possess stronger magnetic characteristics, making them more suitable for specific applications. For instance, materials like iron, nickel, and cobalt exhibit significantly stronger magnetic properties compared to brass. These alloys are commonly used in scenarios where a higher level of magnetism is required.
Iron-based alloys such as steel contain iron as the primary component and display strong magnetic properties. Nickel and cobalt-based alloys also demonstrate robust magnetism, making them ideal choices for various magnetic applications.
Exploring these alternatives is crucial in identifying the best material for specific magnetic needs. By understanding the unique magnetic properties of different alloys, manufacturers can select the most appropriate material based on their application’s requirements.
Application-Specific Materials
In scenarios requiring precise levels of magnetism or resistance to demagnetization, certain materials may outperform brass. For example, in electrical engineering applications where components need to be non-magnetic or have minimal interference with magnetic fields, alternative materials like aluminum or stainless steel might be preferred over brass.
Aluminum possesses low density and high electrical conductivity while being non-magnetic. This makes it an excellent choice for applications that demand lightweight non-magnetic components with good electrical conductivity.
Stainless steel contains iron but is known for its corrosion resistance and durability while maintaining a lower level of magnetism compared to other ferrous metals. It is often utilized in environments where resistance to rust and corrosion are crucial factors alongside specific magnetic characteristics.
Iron-based alloys
Safety Considerations When Handling Brass
Sharp Edges and Heavy Weight
It’s crucial to consider safety protocols. Brass can have sharp edges due to machining processes, making it important to handle with care. It is a heavy material, which can pose risks if mishandled or dropped. These factors make proper handling techniques essential.
Brass components such as sheets, rods, or machined parts may have sharp edges resulting from cutting or shaping processes during manufacturing. It’s important to be cautious when working with these items because the sharp edges can cause cuts or injuries if not handled carefully. Moreover, due to its weight, lifting heavy brass materials without proper technique could lead to strains or accidents.
Proper ventilation and protective gear are necessary when working with brass in various forms. This includes wearing gloves and eye protection when handling brass components that might have sharp edges. Respiratory protection may be required when sanding or grinding brass materials due to potential exposure to fine particles that could be harmful if inhaled.
Understanding safety considerations is essential for preventing accidents and injuries related to brass handling. By following safety guidelines and using appropriate equipment such as gloves and goggles, individuals can minimize the risk of injury while working with this material.
Enhancing the Magnetic Properties of Alloys
Heat Treatment for Enhanced Magnetic Properties
Alloys, including those similar to brass, can have their magnetic properties improved through techniques like heat treatment. By subjecting these materials to controlled heating and cooling processes, it’s possible to alter their internal structure and enhance their magnetic characteristics. For instance, specific treatments can align the atoms within the alloy in a way that increases its responsiveness to magnetic fields. This is particularly important in applications where magnetic properties are crucial, such as in the manufacturing of electrical components.
Heat treatment has been extensively researched and developed with a focus on improving the magnetic properties of alloys for various industries. These efforts aim to optimize the performance of these materials for specific applications by tailoring their response to magnetism. The goal is not only to increase paramagnetic metals’ suitability for use in diverse fields but also to expand possibilities for new technologies and products.
Research on Alloy Magnetic Characteristics
Research into enhancing alloy magnetic properties holds significant promise for advancing numerous industries. For example, advancements in this area could lead to more efficient electric motors or generators due to improved magnetically responsive alloys used in their construction. Innovations might enable better-performing electromagnetic devices with enhanced capabilities thanks to superior alloy-based components.
This research opens up vast potential across different sectors by enabling manufacturers and engineers access to a wider range of materials with tailored magnetic attributes suitable for specific applications. As a result, there’s an increased likelihood of developing highly specialized products that offer superior performance compared to existing alternatives currently available on the market.
Conclusion and Summary on Brass Magnetism
You’ve now uncovered the intricate relationship between brass and magnetism. While brass itself is not magnetic due to its composition, alloying can introduce magnetic properties for specific applications. Understanding the fundamentals of magnetism and how alloying affects materials has shed light on the unique characteristics of brass in various industries. As you consider safety precautions and alternative materials, remember that brass can be tested and enhanced to suit specific magnetic needs.
Now that you grasp the complexities of brass magnetism, explore how this knowledge can be applied in your own projects or industries. Whether it’s optimizing magnetic properties or considering safety measures, integrating this understanding into your work can lead to innovative solutions and improved outcomes. Embrace the potential of brass in magnetism and continue to explore its possibilities in your endeavors.
Frequently Asked Questions
Is brass a magnetic material?
No, brass is not a magnetic material. It is considered non-magnetic due to its composition, primarily consisting of copper and zinc. While it contains some elements that are ferromagnetic, the overall structure of brass does not exhibit magnetic properties.
How can I test if brass is magnetic?
You can easily test the magnetic properties of brass using a simple magnet. If the magnet does not attract or interact with the brass material, then it confirms that the brass is non-magnetic in nature.
What are common uses of brass in industry?
Brass finds wide applications in various industries such as plumbing fittings, musical instruments, decorative hardware, and electrical components. Its excellent malleability and corrosion resistance make it a popular choice for these applications.
Can alloys be made to exhibit magnetic properties similar to iron or steel? (ferromagnetic metals)
Yes, through alloying processes involving specific materials like iron or nickel into non-magnetic base metals like copper or aluminum, alloys can be created with enhanced magnetic properties suitable for various industrial applications.
Are there safety considerations when handling brass?
While generally safe to handle, precautions should still be taken when working with brass due to potential hazards associated with metalworking activities such as sharp edges from machining operations and exposure to metal dust during processing.